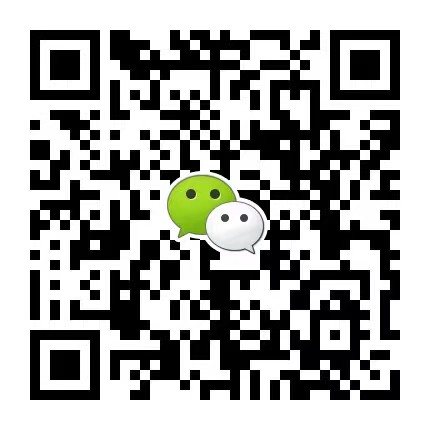
发布日期:2025/6/28 20:49:48 访问次数:33
精密无缝钢管作为高端制造业的关键基础材料,其切割质量直接影响后续产品的性能和可靠性。当前工业领域主要采用五类切割技术,各有其独特的物理原理和适用范围,可满足不同场景对切割精度、效率和质量的差异化需求。
激光切割通过聚焦高功率密度激光束(通常达10⁶-10⁷ W/cm²)照射钢管表面,使局部区域瞬间熔化或汽化,同时用高压辅助气体(氧气、氮气或空气)吹除熔融物质形成切口。这种非接触式加工方式具有明显的技术优势:
热影响区控制:尽管属于热切割工艺,但现代光纤激光器通过优化脉冲频率和采用氮气冷却,可将热影响区(HAZ)控制在0.1-0.5mm范围内。例如Q345B材质钢管切割时,热影响区可控制在20mm以内15。
精度与表面质量:配备高精度直线电机和CNC系统的激光切割机,可实现±0.1mm的重复定位精度,切口粗糙度达Ra 6.3μm以下,基本无需二次加工。佛山市京锦钢铁的案例显示,其设备切割精度可达±0.5mm,速度超过500米/小时10。
灵活性与效率:可编程特性使其能高效处理复杂几何形状(如异形管口、曲线切割),特别适合小批量多品种生产。自动上下料系统实现24小时连续作业,大幅提升设备利用率。
然而激光切割在厚壁管(>15mm)领域面临挑战:不锈钢等高反射材料存在吸收率突变风险;设备初期投入高达80-200万元;能耗成本显著高于机械切割。因此更适用于壁厚12mm以内、要求高精度轮廓切割的液压缸管、轴承管等场景110。
水射流切割利用超高压泵(通常3800-6200 bar)将水加速至2-3倍音速,混合石榴石等磨料后形成侵蚀力极强的切割流。其“冷切割”特性在精密无缝钢管加工中具有不可替代的价值:
零热影响优势:整个切割过程温度保持在40-60℃,彻底消除热应力导致的材质相变、微裂纹问题。对HRC60高硬度淬火钢管切割时,可保持管端金相组织稳定59。
材料适应性:通过调整磨料类型(石榴石/氧化铝)和粒径(80-120目),可切割碳钢、不锈钢、钛合金等各类材质,壁厚适应范围达3-100mm。尤其适合切割高合金钢、双相不锈钢等对温度敏感的材料2。
切割质量特性:切割锥度约0.5°-1°,表面粗糙度Ra 3.2-12.5μm可调。但切割速度相对较慢,20mm壁厚钢管切割速度约20-40mm/min,且设备需处理磨料回收和废水处理问题59。
水射流切割特别适合航空航天用钛合金管、液压阀块集成管等对热敏感的关键部件。但需注意水流冲击力可达2000N以上,必须设计专用夹具防止管材位移影响精度5。
作为机械切割的代表,锯切通过锯齿的机械力实现材料分离。现代锯切设备已发展出多种形态以适应不同管材规格:
带锯系统:采用单条闭环锯带,通过液压张紧和导向装置保证运行平稳。德国贝灵格等高端品牌可实现切割垂直度0.1mm/100mm,特别适合大口径(>300mm)管材切割。细齿硬质合金锯条(每英寸10-14齿)能有效切割壁厚6-30mm钢管23。
圆盘锯技术:旋转锯片在伺服电机驱动下进行径向进给切割。日本天田公司产品切割φ140×6mm钢管仅需3分钟,效率优于带锯。但大直径锯片(>500mm)存在偏摆控制难题,通常用于外径<200mm管材37。
排管锯创新:革命性地实现多管同时切割(最多12支),通过液压夹紧系统和同步进刀机构,使生产效率提升300%以上。适用于批量定尺切割场景,但设备投资高达150万元以上3。
锯切的核心优势在于无热影响且设备成本低(20-80万元)。但切割速度受限(通常<100mm/min),切口存在0.2-0.5mm毛刺需后续刮削处理。最适合普通精度要求的结构管、输送管大批量生产27。
热切割技术在厚壁管领域仍具应用价值,其技术特性呈现明显差异:
等离子切割:通过电离气体形成10000-30000℃高温等离子弧,熔化金属实现切割。切割速度是火焰切割的3-5倍,30mm壁厚不锈钢管切割速度达400mm/min。但切口存在2-5°锥度,热影响区约0.5-2mm,需预留加工余量29。
火焰切割:依靠氧-乙炔混合气体燃烧(温度约3100℃)和氧化反应切割材料。设备成本最低(5-15万元),但热影响区高达3-8mm,易导致高碳钢管端淬硬裂纹。切割面粗糙度通常为Ra 25-50μm,需后续车削加工79。
这类技术适用于对精度要求不高的厚壁(>30mm)管道预制,如石油平台桩管、压力容器管等。但需注意合金钢管切割后需退火消除应力7。
砂轮切割属于物理磨削切割,通过高速旋转(通常3000-6000rpm)的树脂结合剂砂轮磨除材料。其技术特点鲜明:
设备成本效益:手持式切割机价格仅千元级,半自动机型约2-10万元,投资门槛最低。操作简单,适用于工地现场切割作业15。
切割质量局限:切割垂直度偏差可达0.5-1°,表面粗糙度Ra 12.5-25μm。切割时产生较大径向力,易导致薄壁管(<5mm)变形。粉尘污染严重,需配套除尘系统5。
技术改进方向:新型金刚石涂层砂轮寿命延长3倍,切割φ140×6mm钢管时间缩短至4分钟。自动夹紧装置可减少管材振动,提升切口质量5。
该技术主要作为辅助切割手段,适用于维修现场、样品制备等小规模作业场景。
表:精密无缝钢管主要切割技术特性对比
切割方式 | 热影响区 | 切割精度 | 切割速度 | 适用壁厚 | 设备成本 |
---|---|---|---|---|---|
激光切割 | 0.1-2mm | ±0.1mm | 高速(>500m/h) | <15mm | 高(80-200万元) |
水射流切割 | 无 | ±0.2mm | 低速(20-40mm/min) | 3-100mm | 高(100-300万元) |
带锯切割 | 无 | ±0.1mm/100mm | 中速(50-100mm/min) | 6-30mm | 中(20-80万元) |
等离子切割 | 0.5-2mm | ±0.5mm | 高速(400mm/min) | >5mm | 中(30-100万元) |
砂轮切割 | 无 | ±0.5mm | 中速(切割时间4min/管) | 不限 | 低(0.1-10万元) |
选择精密无缝钢管切割工艺需系统分析四大核心要素,这些因素共同构成了切割工艺决策的技术经济框架。
钢管的化学成分和物理特性直接影响切割方法的适用性:
材料硬度与强度:淬硬钢管(HRC≥50)如GCr15轴承钢,应优先选用水射流或冷锯切。激光切割高碳钢时需采用脉冲模式防止管端淬裂,硬度超过HRC60时锯条寿命急剧下降59。
壁厚适应范围:薄壁管(<5mm)适用高速激光切割;中等壁厚(5-20mm)是带锯和圆盘锯的最佳区间;超厚壁(>50mm)仍需采用多头火焰切割或坡口等离子切割。例如水射流切割100mm厚管需配置380MPa以上超高压系统9。
合金元素影响:含铬>5%的不锈钢存在激光反射风险,需采用蓝光激光器;钛合金等活性金属必须用水切割防止氧化;高碳钢(如45#)火焰切割时需预热至300℃防止裂纹79。
不同终端应用对管端质量的要求差异显著:
尺寸精度等级:普通结构管(H10-H12级)可采用锯切;液压缸管要求H7-H8级精度,需激光或水切割;半导体用气动管圆度要求≤0.01mm,必须珩磨后水切割4。
表面完整性:焊接管端需控制Ra<3.2μm以保障密封性;高压油缸要求滚压后Ra<0.25μm,激光切割后需去氧化层;航空航天管要求100%无微裂纹,水切割是最佳选择4。
几何精度指标:管端垂直度偏差需<0.5°/100mm,否则影响焊接质量;锯切需动态补偿系统控制锯偏;激光切割锥度需通过变焦控制310。
生产规模决定工艺路线的经济合理性:
批量规模效应:单件小批(<50件)适合激光或水切割;大批量(>5000件)应选用排管锯或圆盘锯生产线。如冷拔缸管生产线配置6轴圆盘锯,每支切割循环仅15秒6。
综合成本构成:设备折旧(激光机>300万元)、工具消耗(锯条0.5-2元/cm)、能源成本(水切割>30kW/h)需整体核算。焊接管DOM成本约2000-3500美元/吨,无缝管SCD达3000-5000美元/吨4。
自动化集成度:汽车行业要求连线生产,需配置机械手上下料;激光切割可与AGV物流系统集成;水切割因节拍慢(20mm/min)常作为独立工序10。
切割工艺需置于整体制造链条中评估:
焊接准备需求:需焊管端应预留30°±2°坡口,火焰切割需二次加工,而激光-坡口复合机能一次成型3。
热处理状态:调质态钢管(如42CrMo)切割时需控制温度<200℃,防止硬度下降;固溶态不锈钢应避免热切割引[Citation:7]9。
环境合规要求:砂轮切割粉尘需符合OSHA 5mg/m³标准;水切割磨料需沉淀处理;激光切割烟尘需配备除尘系统58。
不同应用领域对精密无缝钢管的性能要求差异显著,需针对性选择切割工艺组合。基于行业实践和技术经济分析,形成以下选型建议。
液压缸筒、气动缸体等压力容器用管对切割质量要求最为严苛,典型代表为SCD(无缝冷拔刮削滚压抛光管)和DOM(焊接冷拔管):
高压液压缸(≥35MPa):必须选用激光切割+管端珩磨工艺。激光保证φ140×10mm缸管切割垂直度≤0.1°,珩磨实现Ra<0.1μm镜面效果。如飞机起落架作动筒需承受70MPa压力,切割热影响区必须<0.2mm410。
中压系统(20-35MPa):可采用水切割DOM管,如卡特彼勒挖掘机油缸。切割后需滚压强化,使表面硬度达HB150-200。切割速度控制在40mm/min保证管端圆度≤0.1mm4。
气动精密管:薄壁(1-3mm)不锈钢管优先选用光纤激光切割,采用氮气保护防止氧化。半导体设备用管需水切割后电解抛光,达到Ra<0.4μm超光滑表面8。
淬硬钢管(HRC50-65)常见于轴承、模具等领域,其切割需特殊工艺:
整体解决方案:首选水射流切割,配置400MPa增压系统。切割GCr15轴承管(HRC62)时,采用0.8mm喷嘴和120目石榴石磨料,速度15mm/min可保证无微裂纹59。
替代技术方案:当无法采用水切割时,应使用金刚石涂层砂轮配合冷却液切割。切割参数:线速度≥35m/s,进给量0.05mm/rev。如SKS3模具钢切割后需-70℃深冷处理消除应力5。
禁忌工艺:绝对避免火焰切割,否则必然导致管端淬裂;激光切割需经退火处理,但导致硬度下降HRC5-109。
光学仪器、半导体设备用管要求μm级精度:
纳米级精度场景:如ASML光刻机导轨管,要求直线度≤0.02mm/m。必须采用珩磨管(Honed Tube)配合水切割,切割后电解抛光实现Ra<0.1μm4。
精密传动部件:机床主轴用管(φ50×5mm)适用激光精密切割,采用飞切技术保证端跳≤0.005mm。切割后需低温时效处理消除残余应力410。
特殊材质处理:钛合金管切割需在水介质中进行,防止氧化层生成;陶瓷复合管采用超声波辅助水切割9。
建筑、输送系统等结构用管侧重效率经济性:
大批量生产:配置自动排管锯系统,如德国KASTO自动线可同时切割12支φ89×4mm钢管,每支耗时仅90秒。采用硬质合金锯片寿命达800切割米37。
现场修配场景:便携式等离子切割机是优选,如海宝Powermax105可切割50mm厚管。配合坡口导轮可实现30°焊接坡口一次成型9。
经济型方案:普通碳钢管(Q235B)可采用砂轮切割,成本最低。但需预留3mm加工余量,后续需车削端面1。
精密无缝钢管切割技术正朝着高精度、智能化、绿色化方向演进。通过系统分析现有技术路线并展望未来趋势,可为产业升级提供决策参考。
基于技术参数和经济指标构建的评估体系显示:
表:精密无缝钢管切割工艺综合性能评级
评价维度 | 激光切割 | 水射流切割 | 带锯切割 | 等离子切割 | 砂轮切割 |
---|---|---|---|---|---|
切割精度 | ★★★★★ | ★★★★☆ | ★★★☆☆ | ★★★☆☆ | ★★☆☆☆ |
表面质量 | ★★★★☆ | ★★★★☆ | ★★★☆☆ | ★★☆☆☆ | ★★☆☆☆ |
热影响控制 | ★★★☆☆ | ★★★★★ | ★★★★★ | ★★☆☆☆ | ★★★★★ |
厚壁能力 | ★★☆☆☆ | ★★★★★ | ★★★★☆ | ★★★★★ | ★★★☆☆ |
设备成本 | ★★☆☆☆ | ★★☆☆☆ | ★★★☆☆ | ★★★☆☆ | ★★★★★ |
运行成本 | ★★★☆☆ | ★★☆☆☆ | ★★★★☆ | ★★★☆☆ | ★★★★★ |
效率指数 | ★★★★★ | ★★☆☆☆ | ★★★★☆ | ★★★★☆ | ★★★☆☆ |
注:★数量代表性能等级,越多表示越优
激光切割在薄壁管领域综合得分最高(23★),水射流切割在厚壁特殊材料领域不可替代(24★),带锯切割在常规应用中经济性最优(22★)。等离子和砂轮切割在特定场景仍具应用价值1410。
前沿技术正推动切割工艺向更高层次发展:
复合加工技术:激光+水导引切割技术实现100mm厚管切割,热影响区<0.1mm;锯切-倒棱复合机实现管端35°坡口一次成型,效率提升40%310。
数字孪生系统:西门子CutSim平台通过物理建模预测切割变形,φ219×8mm钢管切割精度提升至±0.05mm。大数据分析锯条寿命,优化切割参数提升30%效率10。
绿色制造工艺:水切割磨料循环利用率突破85%;激光器光电转换效率达45%;干式切割技术减少切削液污染89。
超快激光技术:皮秒激光切割高反材料(铜、铝管)效率提升5倍,切口无熔融层。飞秒激光可实现陶瓷、蓝宝石等脆性材料精密切割10。
建议采用三级决策树实现科学选型:
材质与状态判断
硬度>HRC50或热敏感材料→水切割
常规材料→进入下一级
精度与效率权衡
精度要求H7级以上或Ra<1.6μm→激光/水切割
普通精度→考虑锯切
经济性优化
大批量生产→自动排管锯
小批量多品种→激光切割
现场维修→砂轮/便携等离子
例如高精度液压缸管(SCD材质)选型路径:常规材料→精度要求H7→小批量→选择激光切割+后续珩磨410。
通过以上系统性分析可见,精密无缝钢管切割技术已形成多元化技术路线。未来五年,随着激光器功率提升和超高压水射流成本下降,精密冷切割占比将提升至60%以上。同时人工智能将实现切割参数的实时优化,使加工质量波动降低70%。制造企业需构建切割工艺数字孪生系统,动态优化工艺路线,在质量、效率和成本间取得最佳平衡。